What are the advantages of ringlock scaffolding?
In recent years, in the Chinese construction market, ringlock scaffolding has gradually become the main Construction Scaffold, and cuplok scaffolding has gradually disappeared from everyone's field of vision. Ringlock scaffolding is a new type of building a support system with diverse functions. According to different construction requirements, it can be constructed with different shapes and load-bearing capacity of single and group frame sizes, double-row scaffolds, support columns, support frames, and other functions. equipment.
Ringlock scaffolding is widely used in construction, municipal roads and bridges, rail transit, energy and chemical industry, aviation, and shipbuilding industry, large-scale cultural and sports activities temporary construction facilities, and other fields.
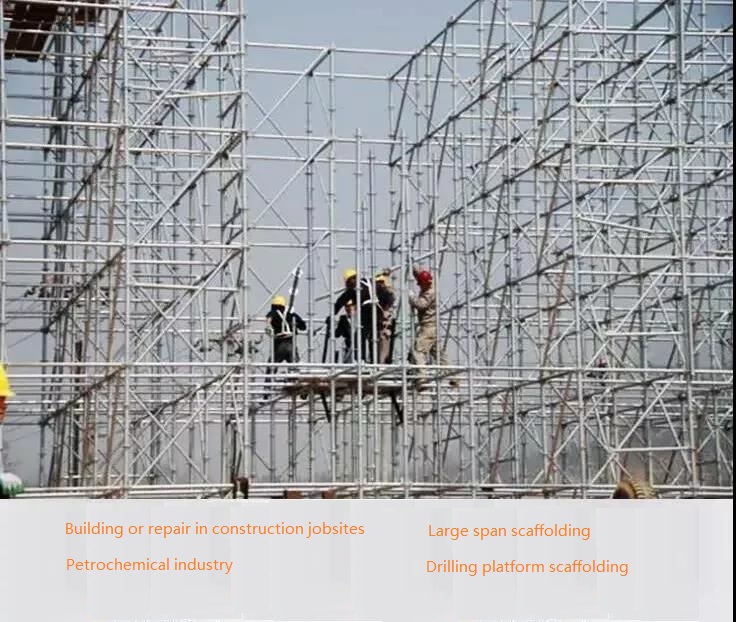
1. The main accessories of the scaffolding
The main accessories of Ringlock scaffolding are vertical, horizontal, diagonal brace, adjustable base, U-Head Jacks, etc.
Vertical: A circular connecting plate that can be buckled with 8 direction joints is welded every 0.5 meters. One end of the vertical is welded with a connecting sleeve or an internal connecting rod to connect the vertical.
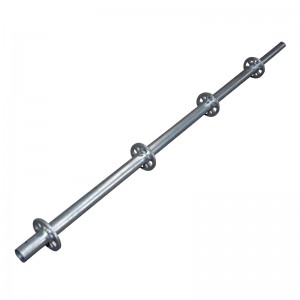
Horizontal: It is composed of a plug, a wedge pin, and a steel pipe. The crossbar can be buckled on the vertical rod disc.
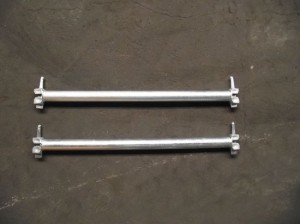
Diagonal Brace: The diagonal rod is divided into the vertical diagonal rod and horizontal diagonal rod. It is a rod to ensure the stability of the frame structure. The two ends of the steel pipe are equipped with buckle joints, and the length is determined by the spacing and a step distance of the frame.
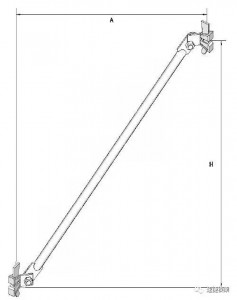
Adjustable base: a base installed on the bottom of the frame to adjust the height of the scaffold.
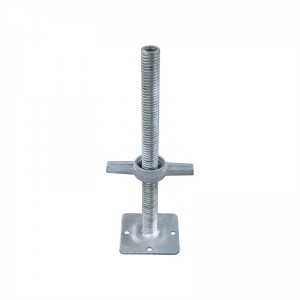
Adjustable U-head Screw Jacks: a screw jack installed on the top of the pole to accept the keel and adjust the height of the supporting scaffold.
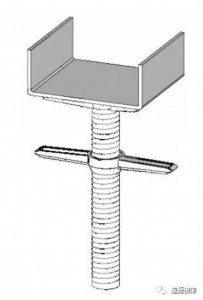
2. Installation method of new type ringlock scaffolding
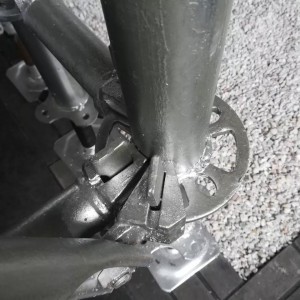
When installing, you only need to align the horizontal connector to the position of the ringlock plate, then insert the pin into the ringlock hole and pass through the bottom of the connector, and then hit the top of the pin with a hammer to make the arc surface on the horizontal joint tightly integrated with the vertical stantard.
The Vertical Standard is made of Q345B low-carbon alloy structural steel, Φ60.3mm, and the wall thickness is 3.2mm. The maximum load of a single standard is 20 tons, and the design load can be up to 8 tons.
The horizontal is made of Q235 material, the middle is 48.3mm, and the wall thickness is 2.75mm
The diagonal brace is made of Q195 material, Φ48.0mm, and the wall thickness is 2.5mm; the disc is made of Q345B material, and the thickness is 10mm; this system is equipped with a special vertical diagonal brace, instead of steel pipe fastener type vertical scissor brace, vertical rod synchronous design, opposite The verticality of the rod is synchronized to correct the deviation. According to the current engineering experience, the supporting scaffold in the ringlock can be erected at a height of 20-30 meters at one time.
3. The detailed breakdown of the scaffolding
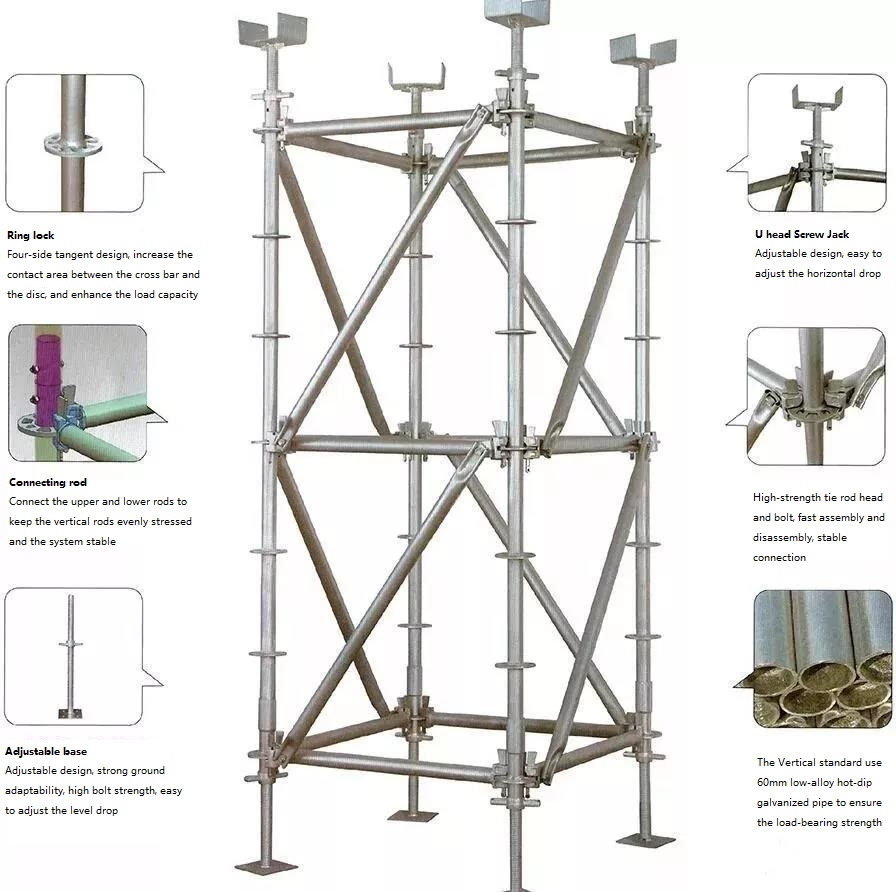
4. Why is the ringlock scaffolding more and more popular?
Advanced technology: The ringlock connection method has 8 connections for each node, which is an upgraded product of the scaffolding currently used worldwide.
Raw material upgrade: The main materials are all made of vanadium-manganese alloy structural steel, whose strength is 1.5-2 times higher than that of traditional scaffolding ordinary carbon steel pipe (GB Q235).
Hot Zinc Process: The main components are treated with an internal and external hot-forged zinc anti-corrosion process, which not only improves the service life of the product, but also provides a further guarantee for product safety, and at the same time, it is beautiful and beautiful.
Large bearing capacity: Taking the heavy support frame as an example, the single standard (060) allows the bearing load to reach 140KN.
Less consumption and lightweight: In general, the spacing of the poles is 1.2 meters, 1.8 meters, 2.4 meters, and 3.0 meters. The stride of the crossbar is 1.5 meters. The maximum distance can reach 3 meters, and the step distance can reach 2 meters. Therefore, the consumption under the same support area will be reduced by 60%-70% compared with the traditional cuplok scaffolding support frame.
Fast assembly, convenient use, and cost-saving: due to the small amount and lightweight, the operator can assemble more conveniently, and the efficiency can be increased by more than 3 times. Each person can build a 200-300 cubic meter frame per day. Comprehensive costs (set-up and disassembly labor costs, round-trip transportation costs, material rental costs, mechanical shift fees, material loss, wastage costs, maintenance costs, etc.) will be saved accordingly. Generally, it can save more than 30%.
5. Compare to the cuplok scaffolding, what are the advantages ringlock scaffolding has?
1. Low purchase cost
Compared with the cuplok scaffolding, it saves more than 1/3 of the steel consumption. The reduction of steel consumption is in line with the national policy orientation of a low-carbon economy, energy-saving, and emission reduction. In addition to huge social benefits, it also provides a reliable and guaranteed formwork support system for construction units, which greatly reduces the purchase cost of enterprises.
2. Low tower construction cost
The ergonomic efficiency of the steel pipe fastener scaffolding facility is 25-35m³/man-day, the ergonomic efficiency of demolition construction is 35-45m³/man-day, the ergonomic efficiency of the cuplock scaffolding facility is 40-55m³/man-day, and the demolition ergonomic efficiency is 55-70m³/ The work efficiency of the ringlock scaffolding facility is 100-160m³/man-day, and the work efficiency of demolition is 130-300m³/man-day.
3. Long product life
All are treated with hot-dip galvanizing process, with a service life of more than 15 years.